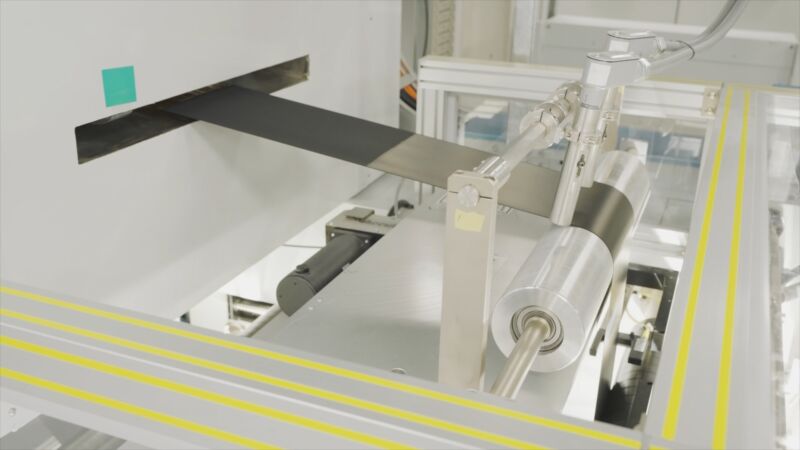
GM/Honda
BROWNSTOWN, Mich.—Today, a joint venture between General Motors and Honda Motor Company, named Fuel Cell System Manufacturing LLC (FCSM LLC), officially started producing its one and only product—a fuel cell system—on a commercial scale. FCSM officially began in January of 2017 with an initial investment between GM and Honda of $85,000,000. Now, the 70,000-square-foot (6,500 m2) facility in Brownstown, Michigan, houses 80 employees and enough robots, clean rooms, and all sorts of high-tech equipment to make Ironman blush.
FCSM managing to build fuel cells quickly, reliably, and cost effectively is what’s new here, not the fuel cells themselves. And, according to Tetsuo Suzuki, vice president of FCSM LLC, that proved the biggest challenge. “Our fuel cell system consists of more than 300 individual cells [307 in total], each cell is composed of very expensive materials. If there is a defect in even one cell, the entire stack would be unusable,” Suzuki said. “Therefore, we designed all of our mass production processes with a zero-defect mindset.” Adding, “We introduced quality control into every process.”
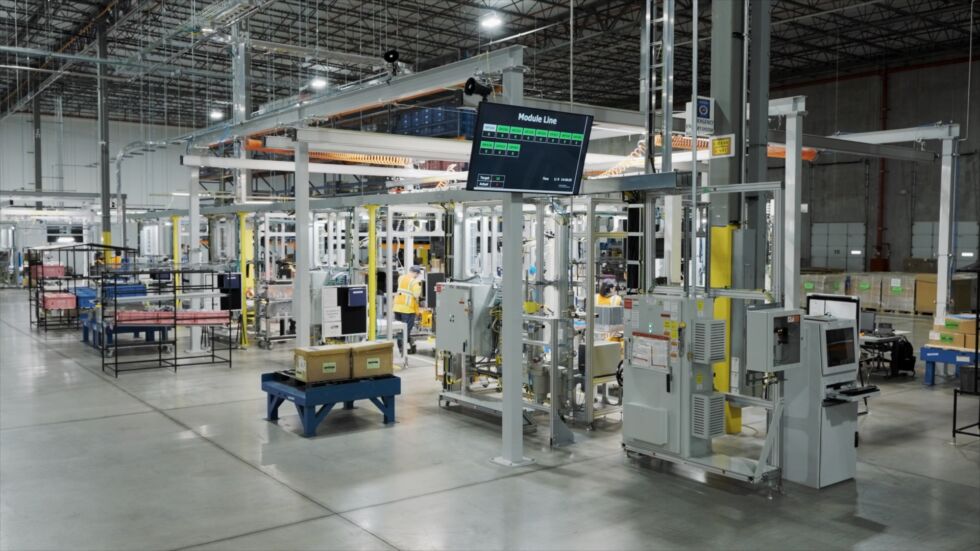
GM/Honda
How to build a fuel cell
More specifically, each cell consists of several parts, starting with two different liquids that FCSM calls “inks.” One ink forms an anode, the other, a cathode. FCSM then pours each liquid onto a carbon-fiber paper, which it then heats to dry. It then precisely cuts these two different papers into shape and bonds them together to form what it calls a unitized electrode assembly, or UEA; the cathode on one side, the anode on the other. Both of the anode and cathode sheets are black, but the cathode sheet is gloss, and the anode sheet is matte.
Separately, FCSM precisely forms a thin sheet with specific channels for hydrogen and oxygen to pass through. It calls this sheet a bi-polar plate, or BPP. FCSM considers any further detail of the BPP proprietary and kept mum when asked about thickness, materials, and so on. The BPP and UEA then meet and bond together, forming one cell. FCSM does that 306 more times, stacks all of them tightly together in a case, uses more than a mile of sealant to keep it from leaking, and voila, one completed fuel cell leaves the line.
As all of that assembly takes place, 50 cameras monitor progress, constantly keeping an extremely close watch on each step of the process to ensure nothing gets contaminated. To that end, the few humans who do play a role here must first put plastic booties over their shoes and take an air shower, as this portion of assembly is a clean room. Before considered finished, each fuel cell completes a leak test, but using helium, not hydrogen. FCSM claims that helium pumped through the stack “at a certain rate” correlates to hydrogen, all without the risk of a highly flammable gas leaking in a manufacturing plant.
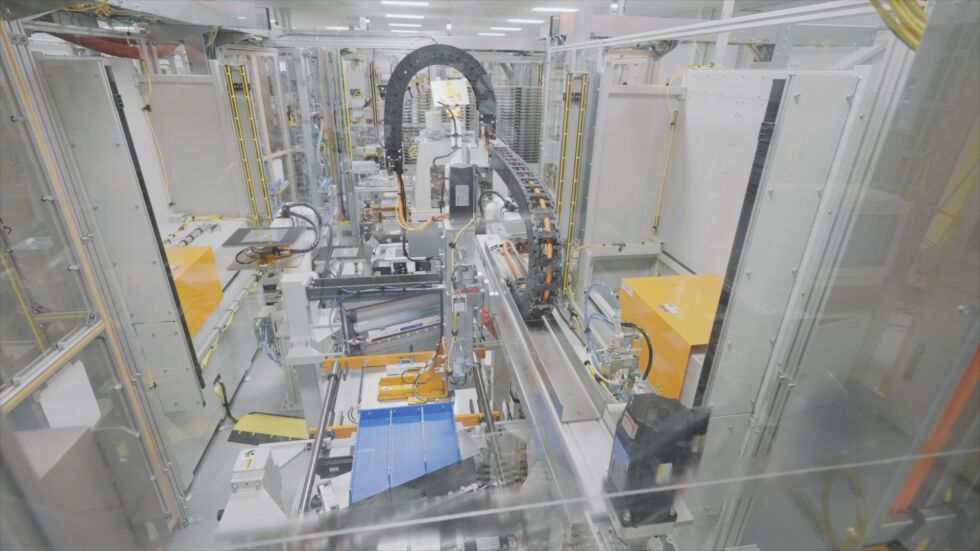
GM/Honda
Assuming it passes the leak test, FCSM finally submits the fuel cell to a roughly one-hour-long break-in procedure, which prepares it to start making power. Once completed, the fuel cell either goes next door to start life as a GM HydroTec Power Cube, or it heads to Honda’s Performance Manufacturing Center outside of Marysville, Ohio, to start life as a, well, “Fuel Cell Module.” Honda failed to name its version of the joint venture final product just yet.
FCSM did not divulge much about power outputs or other details. But according to Jay Joseph, vice president of sustainability and business development at Honda, “These systems are modular. We can add 250kW with each additional module.” That gives us a good foundation to work with.
Once each module or Power Cube leaves FCSM premises, this GM and Honda co-owned, co-developed product starts to compete with itself. Despite both brands speaking highly of each other and this technical partnership that began in 2013, both brands look to pursue similar lines of business.
But, at least to start, we need not worry about too much friction between these alternative energy-seeking partners.
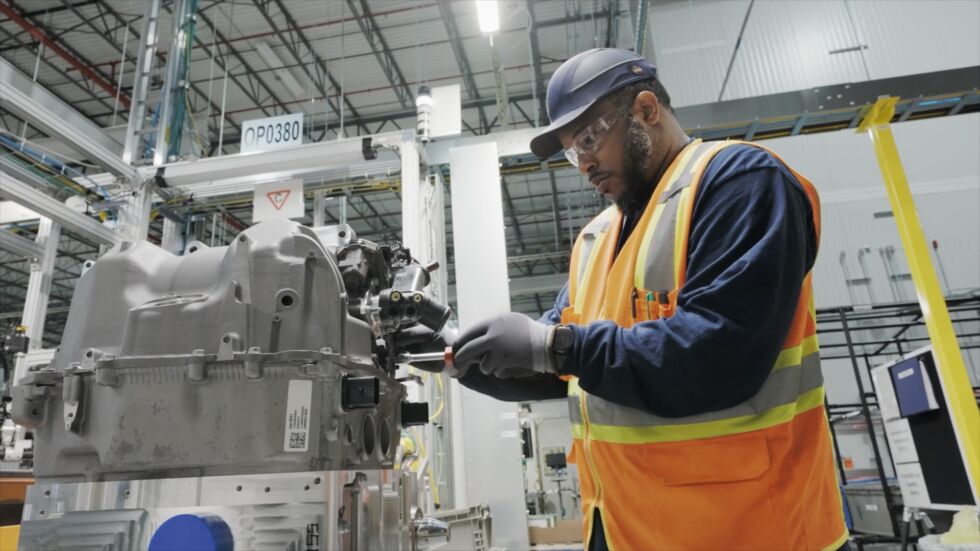
GM/Honda
Mining trucks to big rigs to generators
Hydrogen fuel cells work well for large vehicles. According to Charlie Freese, executive director Global HydroTec GM, “Fuel cells uniquely fill the need of the heaviest, most capable vehicles that carry the largest payloads the longest distances and also require fast refueling.” Freese added, “These systems can be applied to everything from mining equipment to Class 8 trucks [semi-trucks or tractor trailers] to power generators.”
Freese proceeded to discuss a collaboration with Autocar, a truck manufacturer, to use the fuel cell to power cement trucks, refuse haulers, terminal tractors, and class eight semi-trucks. And, when asked later, folks at GM said it would take “maybe two” Power Cubes to propel a single truck of this size. Taking that line of thought further, Freese also mentioned a collaboration with Komatsu: “The Komatsu mine haul truck, it will have two megawatts of hydrogen fuel cell power on board to electrify the 930E 320-ton dump truck.” GM said it would take “more like 20” Power Cubes for each mining truck.
That’s not to say that GM doesn’t plan to incorporate fuel cell technology into passenger cars, but Freese brought forth the idea this way:
“GM views fuel cells as being a complement to lithium-ion battery technology,” Freese said. “Each has a role to play. In fact, almost every fuel cell application you can point to has a battery involved in helping make the propulsion system function as a hybrid.” In the past, Freese has told Ars that applications like heavy trucking along predictable routes make the most sense for hydrogen in the near term rather than trying to build out infrastructure for an entire nation’s passenger vehicles.
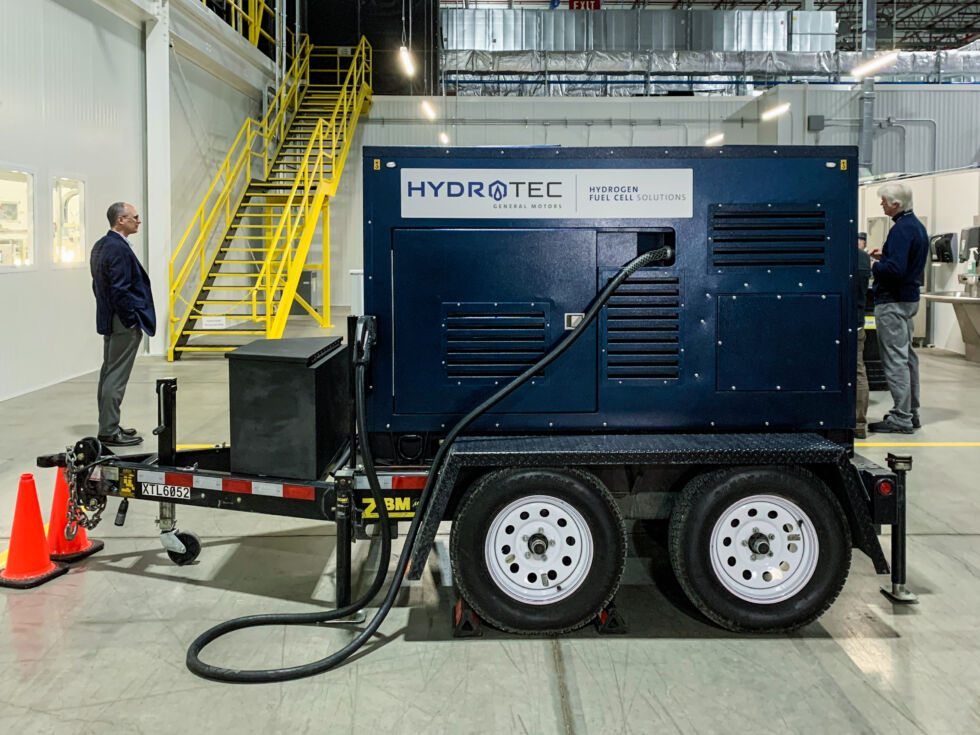
Robin Warner
Honda is building a passenger fuel cell EV
Conversely, Joseph reminded us that the upcoming Honda CR-V fuel cell electric vehicle, or FCEV, is just a couple months away. Honda will build that version of CR-V at the Performance Manufacturing Center in Ohio and will use the new fuel cell coming out of the FCSM plant. When compared to Honda’s last fuel cell vehicle, the Clarity, Joseph said that “this is a new generation of fuel cell, one generation advanced. It’s lighter, smaller, has more power output, and is significantly more reliable than the previous generation.”
On top of that, Joseph also states this collaborative fuel cell costs one-third less than the Clarity’s unit.
Passenger vehicles make up one of four pillars that Honda sees in its fuel cell future, with commercial trucks, stationary power stations, and construction machinery making up the other three. Ultimately similar to GM but inverted.
Motoring around in hydrogen fuel cell-powered passenger cars en masse still seems a long way away. Battery-electric vehicles have had a big head start and will always be more efficient because of the losses involved in hydrogen production. On that topic—in 2023, the US Department of Energy said it is spending $7 billion to build a series of regional clean hydrogen-generation hubs.
But I feel truly heartened to see an earnest effort to scale up production of a technology that uses an, ultimately, abundant energy source with nothing more than water as exhaust.